Understanding Pressure Gauges: Precision Tools for Safe and Efficient Operations
- joddiemarshall6
- Jun 21, 2023
- 3 min read
Pressure gauges are instrumental in various industrial processes, scientific research, and even in daily life. They serve as the eyes for operators and technicians, allowing them to read pressure levels and ensure system integrity. This article offers a comprehensive understanding of pressure gauges, their types, working principles, and the crucial role they play in modern industry and research.

Understanding Pressure Gauges: An Essential Measuring Tool
Pressure gauges are instruments used to measure the pressure of a fluid (liquid or gas) enclosed by a container. They are designed to reveal the force exerted by the fluid per unit area. This measurement is crucial in industries like oil and gas, HVAC, power generation, water treatment, and manufacturing, where safe and efficient operations depend on the maintenance of specific pressure levels.
A pressure gauge typically includes a dial, a pressure system (like a Bourdon tube, diaphragm, or capsule), a mechanism to translate the pressure into dial reading (like link, lever, and gear mechanism), and a casing to protect the internal parts.
Working Principle: Converting Pressure into Readable Output
Most pressure gauges work on the principle of Hooke’s law. It states that the force needed to extend or compress a spring by some distance is proportional to that distance. When a pressure system (like a Bourdon tube) inside the gauge experiences the pressure exerted by a fluid, it tends to change its shape. This shape change is converted into a rotational movement through a link, lever, and gear mechanism, moving the pointer on a calibrated scale to represent the applied pressure.

Types of Pressure Gauges
There are different types of pressure gauges, each designed to serve specific needs.
Mechanical Gauges
These include bourdon tube, diaphragm, and capsule gauges. Bourdon tube gauges, the most common type, consist of a bent tube that straightens as pressure increases. The motion of the tube is transmitted through a mechanical linkage to the pointer.
Digital Pressure Gauges
Digital gauges use electronic sensors to detect pressure changes and display readings on a digital screen. They are highly accurate, easy to read, and can store readings for future reference.
Differential Pressure Gauges
These measure the difference in pressure between two points in a system. This is critical in filters, pumps, and heat exchangers, where pressure difference indicates the condition of the equipment.
Applications of Pressure Gauges
Pressure gauges play a vital role across various sectors.
Industry
In manufacturing processes, they monitor and regulate the pressure of gases and liquids in tanks and pipelines. Gauges also help detect leaks, a crucial aspect in industries dealing with hazardous substances.
Aviation
Pressure gauges are integral in aircraft to measure various parameters like hydraulic pressure, cabin pressure, and engine oil pressure.
Automobiles
In vehicles, they measure the pressure in the tires, cooling system, and oil pressure, ensuring safe and efficient vehicle operations.
Medical Field
Pressure gauges are used in various medical equipment like oxygen regulators and pressure chambers.
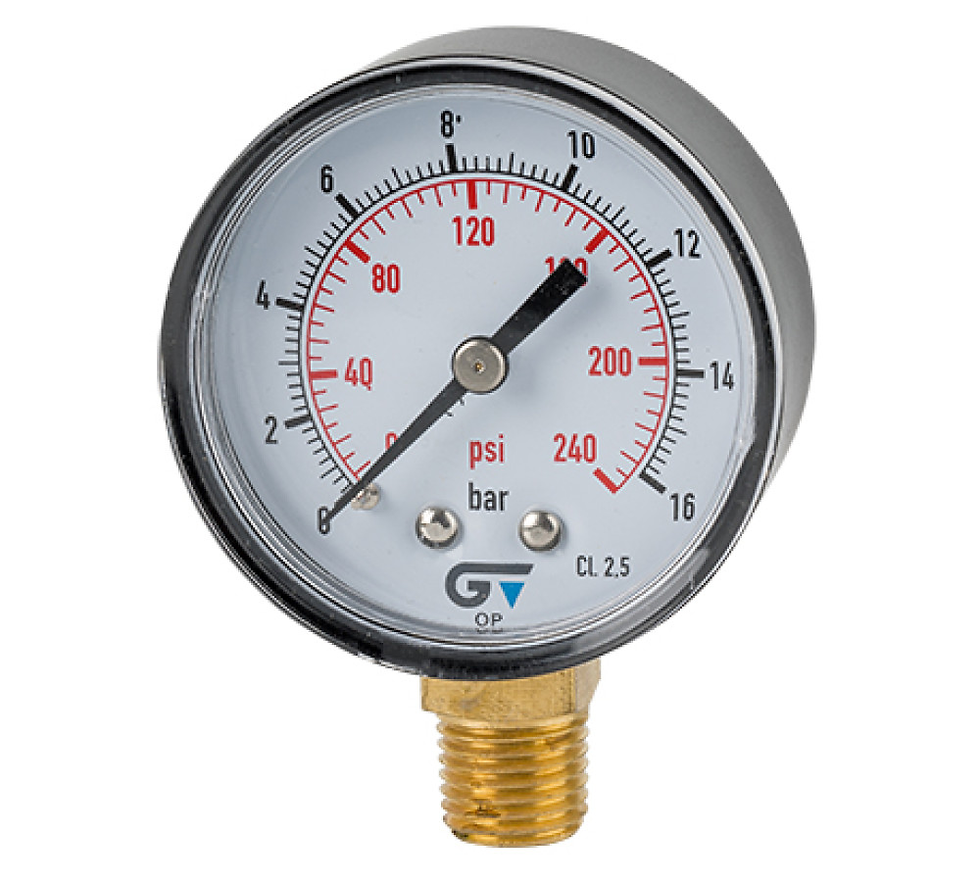
The Importance of Pressure Gauges: Ensuring Safety and Efficiency
Pressure gauges are key to maintaining safety and operational efficiency. An abnormally high or low-pressure reading can signify a problem, allowing preventive measures to be taken before a system failure occurs. Therefore, gauges contribute significantly to preventing accidents, enhancing productivity, and reducing maintenance costs.
In conclusion, pressure gauges are essential tools for industries, research fields, and our daily lives. Their ability to provide precise pressure readings ensures the safe and efficient operation of a myriad of systems and processes. As technology advances, we can expect the development of even more accurate and versatile pressure gauges.
Comments